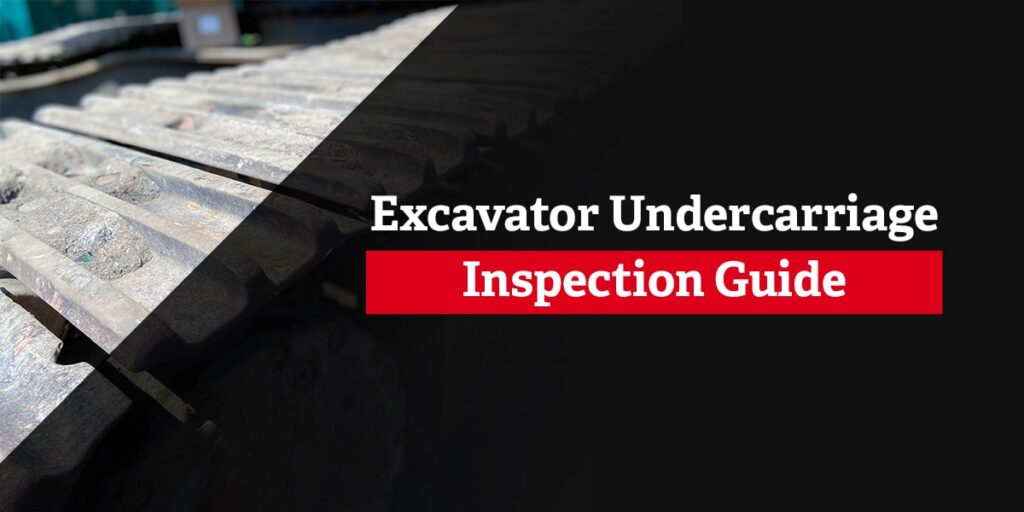
One of the most important components of operating construction equipment is regular maintenance. By conducting frequent inspections, you extend the life span of your equipment and prevent downtime. You can also complete your construction work more efficiently and safely.
An excavator undercarriage is one part you should inspect carefully. The undercarriage supports the machine’s weight and endures extreme wear with each use. It’s essential to check it often to keep it protected.
Here’s a guide on how to check the undercarriage of an excavator.
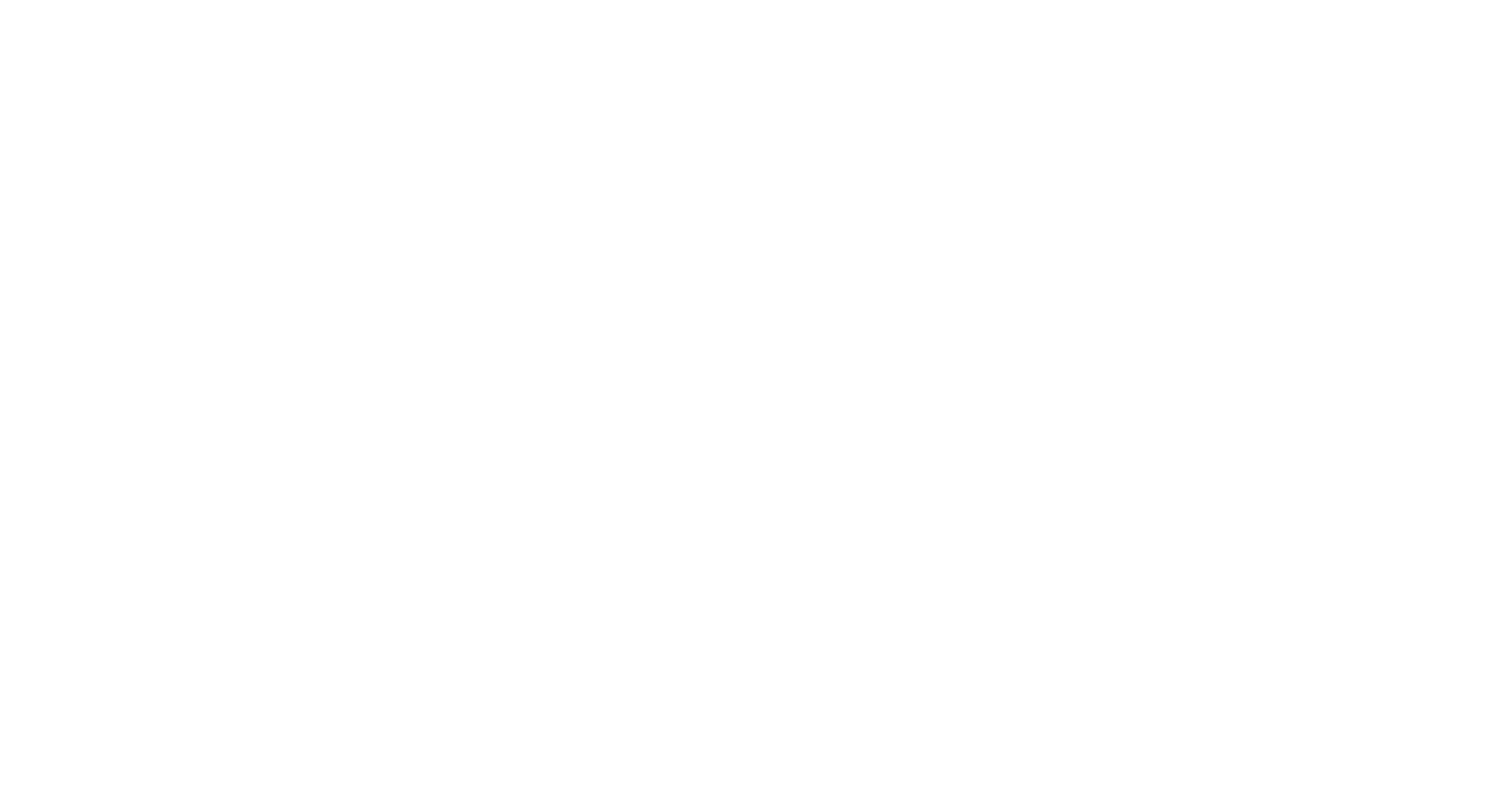
What Is an Excavator Undercarriage?
First things first, an excavator undercarriage is the supporting framework underneath the machine. The wheels get attached to the undercarriage and allow the excavator to move.
There are multiple excavator undercarriage parts, including:
- Track chains: These are the chains and pins on the outside of the undercarriage that contact the surface. They usually consist of steel or other highly durable material.
- Sprockets: Sprockets are circular structures inside the undercarriage. They’re designed with ridges that repel dirt and other materials from reaching track chains.
- Idlers: Usually made by welding, idlers are located at the front and back of the undercarriage. They help relieve tension by distributing weight loads throughout the excavator undercarriage. The idler allows the machine to move forward or backward and keeps the chains aligned during movement.
- Rollers: These wheels are typically located at the top and bottom of the undercarriage. The top rollers brace the chains, while the bottom supports the overall machine’s weight.
The excavator undercarriage functions properly when all parts are in order and work together.
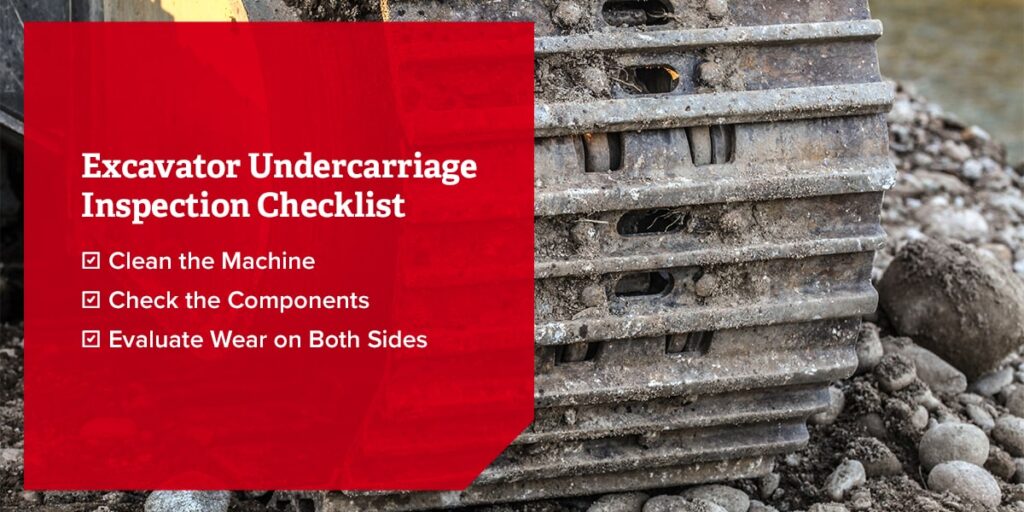
Excavator Undercarriage Inspection Checklist
It’s best to be as thorough as possible when inspecting your undercarriage. Many professionals recommend using a checklist, marking off each part after checking it. That way, you don’t miss any critical features that might be functioning incorrectly.
Here is a checklist for evaluating your excavator undercarriage.
1. Clean the Machine
Before you begin the inspection, take time to clean your undercarriage. The cleaner it is, the more likely you will notice small problems. Too much dirt can keep the machine from functioning correctly. Mud can grind against rollers and gears, stopping the excavator’s movements. So, a dirty machine might cause you to record inaccurate inspection results.
To clean your undercarriage, remove all the extraneous parts and move the machine into a wash area. Clean off extra dirt with a shovel or other tool before rinsing the rest of the machine. Lastly, remove grease and other build-up with a pressure wash.
2. Check the Components
After you clean your machine, it’s time to inspect the different parts in the undercarriage. We recommend starting at one side and checking everything before moving to the next side.
You can follow along with a checklist and mark off each part after inspecting it. If something seems off, make a note as you move along. Here is a sample list of components and what to check for:
- Track chains: Look for loose bolts or nuts within the chains. The chains might also be cracked or bent.
- Sprockets: It’s vital to check sprocket ridges for excess wear. If the teeth look round, the sprockets have been worn down and might need replacements.
- Idlers: Check for cracks, lateral elongations or oil leaks. If you notice any significant damage, you can consider replacing the idlers with new ones.
- Rollers: You should study the top and bottom rollers for cracks and signs of oil leaks.
You can also add additional components to your checklist, but those are some of the major parts of a comprehensive checklist.
3. Evaluate Wear on Both Sides
Lastly, inspect both sides of your undercarriage for wear distribution. Excavator undercarriage wear is often seen best by viewing both sides at once. To do this, look at the left track and the right track and see if one side shows more wear than the other. Note any discrepancies on your checklist. If one side shows significantly more damage, you might think about replacing or repairing it.

What to Do if Your Excavator Undercarriage Is Damaged
Once you complete an excavator undercarriage inspection, you might find that some parts are damaged or showing wear. Mini excavators can last for up to 10,000 hours, but it’s recommended for you to inspect your undercarriage every 1,000 to 2,000 hours. Inspecting your undercarriage regularly can increase your excavator undercarriage’s life expectancy. A mini excavator undercarriage lasts about the same amount as a regular undercarriage. So, if one of your machines is nearing that age, you might consider a replacement soon.
If you notice injuries on your undercarriage and aren’t sure what to do next, there are typically two major options:
- Replace the parts: You could try replacing or repairing parts on a case-by-case basis. For instance, if you notice that one of your rollers isn’t functioning correctly, but everything else is fine, you can order the necessary roller parts and fix it yourself.
- Contact a professional: If you aren’t sure how to address the necessary repair, calling a professional is always a great option. Service providers can diagnose the problem with your undercarriage and replace what you need with ease.
You can also follow other preventative measures to keep the damages from happening in the first place. By following the correct operating procedures and checking your undercarriage regularly, you can keep it running smoothly.
Here are more tips for keeping your undercarriage functioning efficiently:
- Regular maintenance checks: Try to conduct a maintenance check on your undercarriage with the above steps at least once a week. Check the underside of your undercarriage after each usage to make sure dirt or any substance didn’t get lodged in the ridges. The more regular maintenance checks you have, the healthier your machine will be.
- Double-check track tension and alignment: You should also check track tension as often as possible. If the track is too tight, it could harm other machine components. Or, if it’s too loose, it could derail and stop the entire machine’s functioning. Test the tension before each use. If you notice the tension is off, check your operator’s manual for instructions on adjustment or contact a professional for help.
- Travel slowly: One of the quickest ways to wear down your machine is by operating it at high speeds. This puts unnecessary stress on the equipment and causes parts to degrade faster. To keep it running at optimal efficiency, drive it only at recommended speeds and never too far over.
By practicing regular maintenance and treating your machinery properly, you can extend its life span and prevent costly repairs.