hydraulic hammers for excavators
hydraulic hammer for mini excavator
Hydraulic hammers — also called hydraulic breakers — are among the most critical tools across demolition, mining, landscaping and construction sites. Because they are more cost-effective, versatile and productive than gas- or air-powered models, hydraulic breakers are the first choice for experienced contractors and job site supervisors. As high-performing demolition tools, these hammers break up hard surfaces effectively and efficiently when operated by a trained technician.
Learn more about the various types of hydraulic hammers, their different parts and how they work.
What Is a Hydraulic Hammer?
A hydraulic hammer is a tool attachment that can mount on different types of construction equipment, including excavators, backhoes and skid-steer loaders. These hammers use the force created by a piston and pressurized oil to break dense materials like concrete, rock, dirt and clay into smaller, more manageable pieces.
Some of the primary benefits of hydraulic breakers include the following:
- Versatility: Hydraulic hammers provide added flexibility and versatility to an excavator, backhoe or skid-steer loader.
- Durability: This equipment has exceptional durability and long service life.
- Productivity: They can increase work site production with less manual labor.
- Fewer parts: A hydraulic hammer eliminates the need for an air compressor and long hoses.
- Efficiency: Hydraulic equipment has improved fuel efficiency over air-powered models.
- Power: These hammers provide significantly more impact force over traditional designs.
- Safety: Hydraulic hammers make less noise and cause fewer accidents than manually operated hammers.
Hydraulic Hammer Types and Weights
Understanding the different hammer types is vital in choosing the most effective tool for your demolition project. Hydraulic hammer weights, sizes and production speeds differ depending on the specific application. Using the optimal hammer type is crucial for achieving top efficiency for each job.
Hydraulic hammer size configurations include the following:
- Mini hammers: These small breaker designs work well for indoor renovation projects, minor patch jobs and fence-post digging. Their low impact and compact size make them more efficient and much easier to handle than larger models. Working weights range from 400 to 1,200 pounds.
- Medium hammers: Medium-class designs are the most common hammer type and are ideal for jobs requiring frequent hits and high power, like large concrete jobs, utility projects and breaking down large boulders. These breakers deliver excellent efficiency and impact, making them highly versatile for an extensive task range. Working weights on medium-class hammer attachments are generally between 1,900 and 3,700 pounds.
- Large hammers: Large-class hydraulic hammers deliver powerful hits with higher impact and less frequency than smaller models. These designs typically work better for large excavation, mining and demolition projects. Working weights for large breakers usually range from 5,000 to 7,500 pounds.
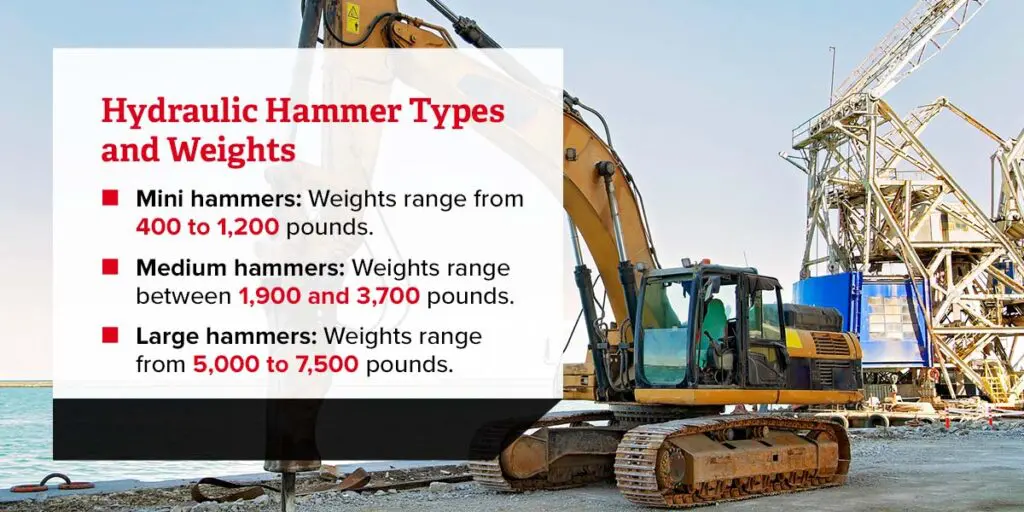
Different Parts of a Hydraulic Hammer
There are two primary types of hydraulic hammers, each with different valve designs. One type uses an inner valve for movement, while the second type uses an outer valve. The internal hydraulic hammer parts are mostly the same in both, as each design uses a cylinder to deliver pressure and a piston to convert energy into a hammering action.
A hydraulic hammer’s components include:
- Control valve and piston: A hydraulic hammer’s control valve and the piston are the only two moving parts. These components are part of the cylinder assembly — the section of the hammer that generates power and creates movement. The valve rotates to control the oil flow’s direction, while the hydraulic hammer piston moves up and down to control the movement of the chisel.
- Head cap: The head cap contains nitrogen gas critical to the hammer’s performance. Steady gas pressure in the accumulator absorbs system spikes and helps generate power.
- Bush: The hydraulic hammer bush provides wear resistance and protects the frame connecting the chisel, preventing outside dirt and debris from entering the unit and obstructing smooth movement.
- Chisel: This part connects to the hammer and performs the actual crushing or breaking of material.
- Chisel pin: The chisel pin keeps the chisel in place during impact.
- Front cover: The front cover secures the chisel and chisel pin.
- Through bolts: These bolts hold the head cap and cylinder together.
- Grease: Hydraulic hammer grease lubricates the chisel to keep the point in peak working order. Insufficient lubrication can shorten the life of the front cap, the chisel pins and the chisel point.
Hydraulic Hammer Chisel Bit Types
Hydraulic breakers can use various chisel tools to perform different breaking actions. Because chisels make direct contact with the materials that need crushing, they wear out over time. Choosing the appropriate chisel type for your application can improve your hammer’s overall life span.
Several examples of the most common types include:
- Moil points: Moil points are the most versatile tools to handle any general breaking application and come standard with many hammers. Moil points are ideal for medium to hard rocks and work well for breaking up concrete with rebar.
- Wedge points: Wedge points are perfect for flat concrete breaking, bedrock excavation, ditch excavations and operations on the face of a slope.
- Blunt chisel: Blunt tools are excellent for demolishing oversized rocks, slabs and heavy boulders. These chisels are among the most durable and stand up to the harshest conditions.
- Conical point: Conical chisels are ideal for various multipurpose applications, including breaking up hard stone, extra-hard rock or reinforced concrete.
How Does a Hydraulic Hammer Work?
The first step in preparing the hammer requires attaching the chisel. Operators connect the hammer to the excavator or other equipment and use the machine’s controls to guide it.
The hammer operates on the principle of Pascal’s law, which states that applying a force to a confined fluid transmits uniformly in all directions throughout the fluid regardless of the container’s shape. Since hydraulic oil is incompressible, it delivers instant power transfer with minimal loss.
The hammering starts in the cylinder’s valve, which controls the oil flow. During the upward stroke, the main valve releases the pressure in the upper chamber through an outlet, causing the lower chamber to push the piston upwards. As the piston reaches the top part of the stroke, the main valve directs the oil flow to the upper chamber and increases the pressure. Because of the accumulated energy, this action causes the piston to move downward.
At the point of impact, the main valve shifts and releases the pressure from the upper chamber, regenerating the upward stroke.